The Process of Creating a Handwoven Carpet
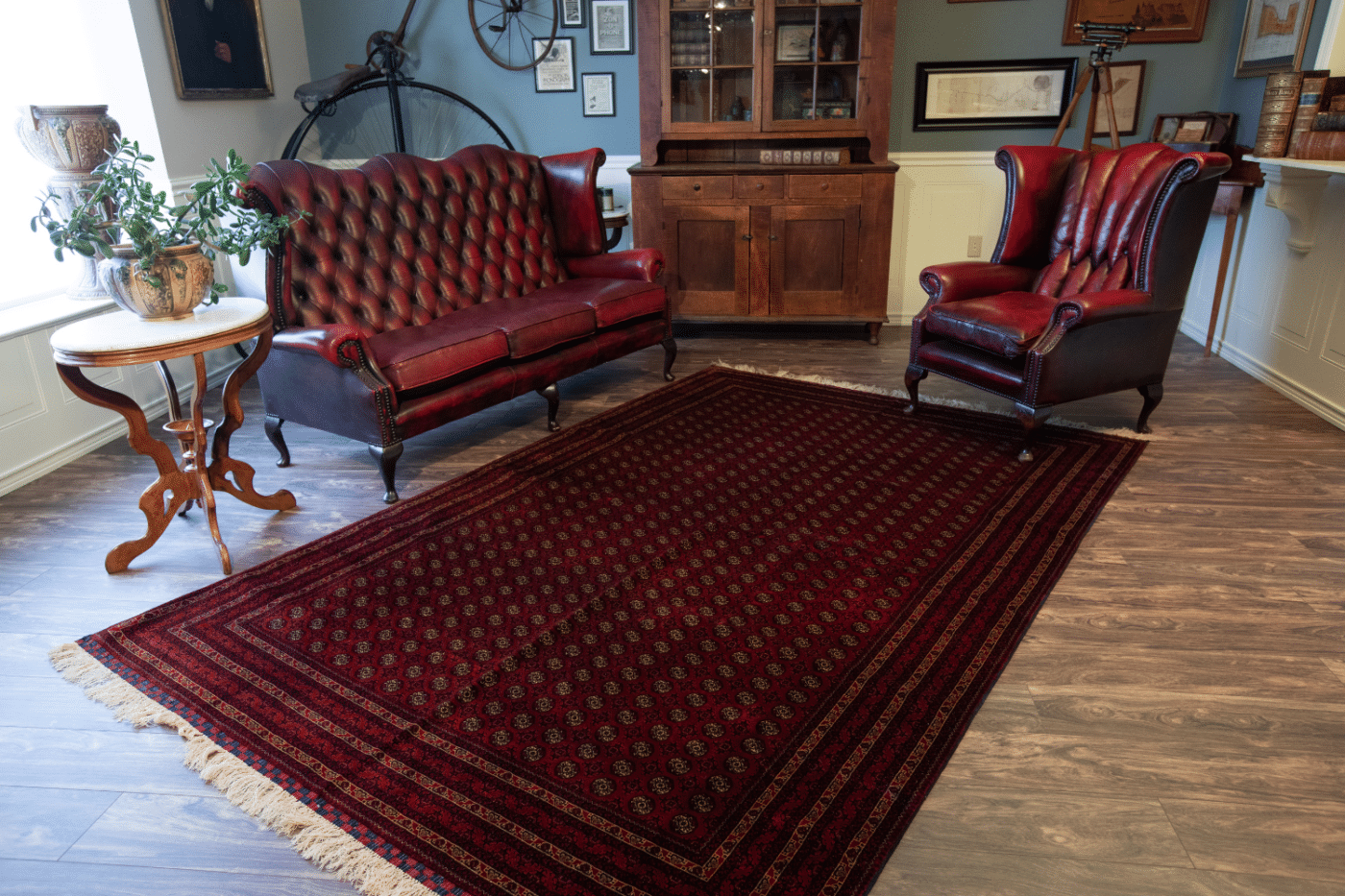
Carpets are beautifully designed pieces that depict art, history, and culture. Knowing that someone took time to craft the rug carefully by hand makes a carpet all the more beautiful. Every single thread and string to make these stunning handwoven carpets is a result of months, or even years, from the weaver. Oftentimes, there will be multiple weavers working on one carpet. The dedication and collaboration inspire each carpet with a unique story, making it not just a floor covering, but a treasured work of art that embodies the spirit and story of the creators.
Background and History of Handwoven Carpets

While the specific origin of handwoven carpets is unknown, they are most famously from Iran, the land of ancient Persia. Persian carpet design has influenced many countries such as Afghanistan and Pakistan. Handwoven carpets are also found in Turkey, India, China, Europe, South America, and many other parts of the world.
Iran
Persian carpets date back to ancient times and are known for their floral and medallion designs. Carpets from Iran are an ancient art form, and these designs include paisley patterns, Herati patterns, and Shah Abbasi designs. Persian carpets are considered national treasures and symbols of Persian artistic heritage. Each pattern relates to a different part of the country. Lachack Toranj are from the city of Isfahan and have a central floral design called the toranj and patterns on the edge called lachack.
Afghanistan
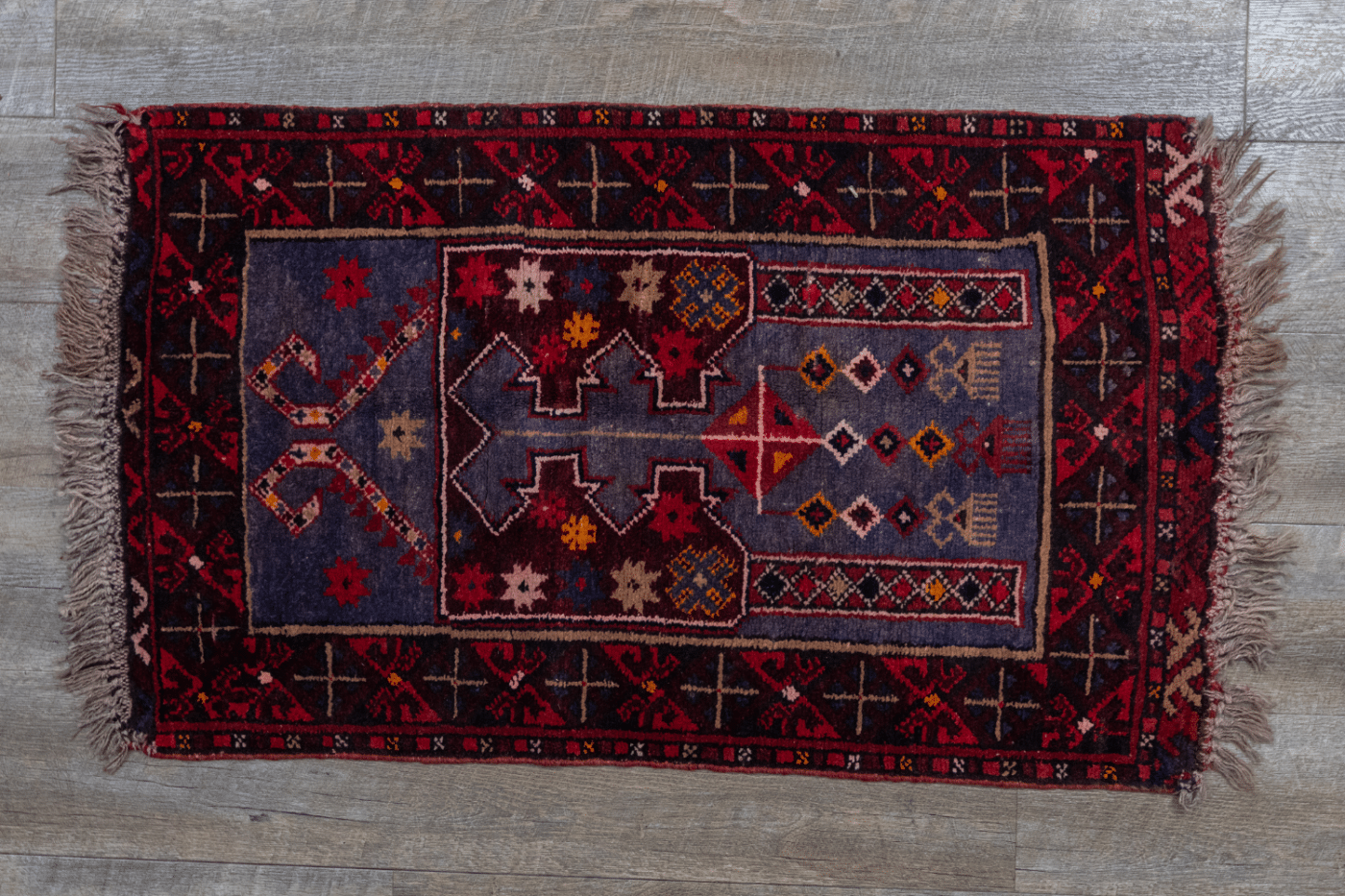
Afghani carpets are influenced by Persian carpets with the addition of their own signatures. Carpet weaving is an important part of Afghan culture and economy, even having designated workshops to create them. Carpets are often a reflection of tribal cultures in Afghanistan, such as Baluchi, Turkmen, and Hazara tribes with each tribe having a signature design. Baluchi rugs are known for their dark colors and tribal patterns, often featuring Muslim prayer rug designs. Afghan weavers are known for their high-quality hand-spun wool as well as their use of natural dyes.
Pakistan
The carpet weaving tradition found in Pakistan can be traced back to the Mughal Empire which brought Persian techniques and designs to the country. Commonly seen designs are floral patterns, medallions, and intricate borders. Different from Afghan carpets, Pakistani rugs use a finer weave. Not only do Pakistani carpets use wool, but they also use silk and cotton which are high-quality materials. Popular types of rugs found in Pakistan include Bokhara rugs, which have a repeating geometric design and rich red backgrounds, and Chobi rugs which feature muted colors and modern designs.
Behind the Loom: A Real-Life Carpet Weaving Tale

Hamid Selami comes from generations of carpet weavers. Since he was young, he could meticulously weave through the ins and outs of the loom, creating intricate patterns and designs that reflected the beauty of his homeland, Afghanistan. Along with his family members, he would work many hours a day to weave a carpet. Explore the art of carpet weaving through the experiences of Hamid, weaving together his personal story with the threads of this ancient art form.
The Carpet Weaving Process for Handwoven Carpets
The process of creating a handwoven carpet includes many steps and is a rigorous process. The steps include dyeing the wool, designing the rug, preparing the loom, weaving the rug, trimming and clipping, and finishing the rug. This process includes many different types of people: shepherds, shearers, wool sorters, spinners, dyers, designers, and weavers. Every role is important in creating the final masterpiece.
Wool for Handwoven Carpets
For carpets, the sheep breeds usually used are Merino, Lincoln, and Karakul because of the quality and characteristics of their wool. Sheeps are then sheared once or twice a year which are then collected in large fleece bundles and sold at local farms or wool markets. Once purchased, this then begins the process of creating the wool.
Scouring
The raw fleece is sorted into high-quality or lower-quality fibers. Grading the wool depends on factors such as fiber diameter, crimp, length, and cleanliness. The wool is then cleaned of any natural oils, dirt, and other impurities. The process of washing the wool is called scouring where it is soaked in warm water and rinsed several times. Upon the completion of scouring, the wool should be removed from all dirt and grease.
Combing, Carding, and Spinning
Before spinning can occur, the wool has to go through combing and carding which aligns the wool fibers in preparation for spinning. Combing occurs when two combs are used and combed from one comb to another until beautiful fibers are created. Carding uses two cardle combs to create webs of slightly tangled fibers. A spindle is used to twist and spin the fibers into yarn to prepare for the next step, dyeing the wool.
Dyeing
The dyeing process includes the wool being put into a dye bath that is heated to let the dye penetrate the fibers. It is immersed in medium temperature and sometimes to temperatures around 140°F, depending on the color, for about one or two hours. It is then rinsed and dried and ready to be created into yarn. There are two different ways to get the dyes, natural and synthetic.
Natural Dyes
Traditional carpet weavers almost always use natural dyes to get the colors for their rugs. Plants and vegetables are used to get different colors. For example, indigo is for blue, madder root and pomegranate is for the color red, and walnut hulls are for brown. Insects like coccus and minerals like lead oxide and iron oxide are used as well.
Synthetic Dyes
Synthetic dyes are chemically produced and, while they offer a broader spectrum of colors and are less likely to fade, they come with significant drawbacks. Chemical dyes are dangerous as they cause burning sensations and blister to the weavers’ fingers due to constant contact with the chemically dyed yarn.
Designing the Handwoven Carpet
While designing the rug is important for custom orders or regions that have specific designs, improvisation is also commonly used. Designs can be drawn out by hand or, nowadays, a computer program will draw out the designs. Designs use a certain color scheme and a specific number of colors. Designs typically include squares, circles, and flowers. Graphs of popular designs are sold in markets and carpet weavers purchase them.
Preparing the Yarn
While designing the rug is important for custom orders or regions that have specific designs, improvisation is also commonly used. Designs can be drawn out by hand or, nowadays, a computer program will draw out the designs. Designs use a certain color scheme and a specific number of colors. Designs typically include squares, circles, and flowers. Graphs of popular designs are sold in markets and carpet weavers purchase them.
Looms
A loom for carpet weaving consists of a frame with two sets of parallel bars, one set fixed and the other adjustable to create tension in the warp (lengthwise) threads. A series of heddles and a shuttle are used to weave the weft (horizontal) threads through the warp, creating the carpet’s structure and design.
Looms are typically large and sturdy, designed to accommodate the size and weight of a carpet. There are two main kinds of looms; a vertical loom and a horizontal loom. Vertical looms, also called upright looms, are common in Persian carpet weaving, and the weaver works from the bottom to the top. Horizontal looms, also called flat looms, are often used by nomadic tribes, and the loom lays flat on the ground while the weaver sits on the ground to weave.
When getting ready to weave, the weaver must pay attention to the loom’s tension, making sure it is not too tight, where the threads might break, or too loose, where the weave will be uneven. The warp threads must then be cut to the desired length of the entire carpet, making sure to add in extra length for tying. The string of yarn is then wrapped around the loom many times, a process that takes many hours. This is a very physical and repetitive process, but it ensures the yarn is specifically placed.
Knots
Knots are tied around pairs of warp threads using short lengths of weft yarn. Each knot begins a pile of the carpet, this is done by working row by row creating knots until the ends of the knots stick up. A pile is the surface layer of yarn that creates texture and patterns in the carpet. There are typically 1,000 knots per square inch. There are two most common types of knots; Persian (Senneh) knots and Turkish (Ghiordes) knots. The Persian knot is an asymmetrical knot with one side of the pile being tighter than the other. This allows for a more detailed design because of its finer structure. A Turkish knot is a symmetric knot that creates an even pile. This allows for the carpet to be more durable and dense.
Wefts
The weft is the thread that is inserted over and under the warp threads to create the carpet. The weft creates the designs, patterns, and textures of the carpet. Weaving techniques involve different ways of interlacing the weft into the warp. The process includes lifting and lowering the warp threads to create an open space, the shed, for the weft thread to pass called shedding, inserting the weft thread through the shed called picking, pushing it into place using a to keep knots tight and secure with a carpet beater called beating, and repeating this process row by row until the carpet is ready to be finished off.
Finishing the Handwoven Carpet
To finish off the carpet, the edges of the rug are secured by binding in order to prevent any part from unraveling. Special scissors are used to get the desired length of the rug and detailed areas are cut shorter to enhance the design. The warp threads left at the ends of the rug are tied into a fringe to give the rug that beautiful addition. But we’re not done yet! The rug is then washed to remove any dirt and excess dye and stretched to ensure it lays flat and keeps its shape. The value of the carpet is then determined by the materials used, the design and its difficulty, and the overall size. The cost of handwoven carpets is expensive, find out what other factors make a rug so expensive.
Where is Hamid Now?

Hamid left Afghanistan and came to the United States as a refugee with his wife, leaving behind his home country and family to start a new life. The Elvan Collection is inspired by Hamid and his journey. His passion lies in continuing the tradition of handwoven rugs while improving the working conditions for the weavers he supports. Hamid has experienced the challenges of this industry firsthand.
At one point, Hamid’s family experimented with chemical dyes because they were cheaper and faster to use. However, they soon discovered the dangers associated with them. “I know people who have lost their fingers,” Hamid says, highlighting the severe effects of using chemically dyed yarn. Unlike natural dyes, chemical dyes leave a harmful residue on the skin. “We couldn’t even finish the carpet we were making; we had to throw it away,” he recalls.
Hamid’s dedication to preserving the art of handwoven rugs extends beyond craftsmanship; it embodies a commitment to ethical practices and the well-being of his fellow artisans. Through the Elvan Collection, each rug not only carries the legacy of tradition but also reflects Hamid’s journey of resilience and advocacy. By choosing an Elvan rug, you support not just a beautiful piece of art, but also a community’s livelihood and a sustainable future for this ancient craft.
Future of Handwoven Carpets

In today’s tech-driven world, finding authentic handwoven carpets is becoming harder. Carpet weaving isn’t just a skill; it’s a complex art that takes time and resources to master. At Orientiq, we’re dedicated to preserving this ancient craft by supporting the talented weavers who keep it alive.
Many of our weavers, often widows or orphans, live in challenging economic conditions. By working with them, along with the help of Hamid and others, we aim to improve their working conditions while maintaining the authenticity and quality of each carpet. This personal connection between the weavers, Orientiq, and you, our valued customer, ensures that every carpet tells a story of tradition, dedication, and empowerment. Here at Orientiq, we are weaving hope, one rug at a time.